Improving Yield Overlay in FOPLP: Advanced Outlier Die Control Technology with Feedforward Lithography
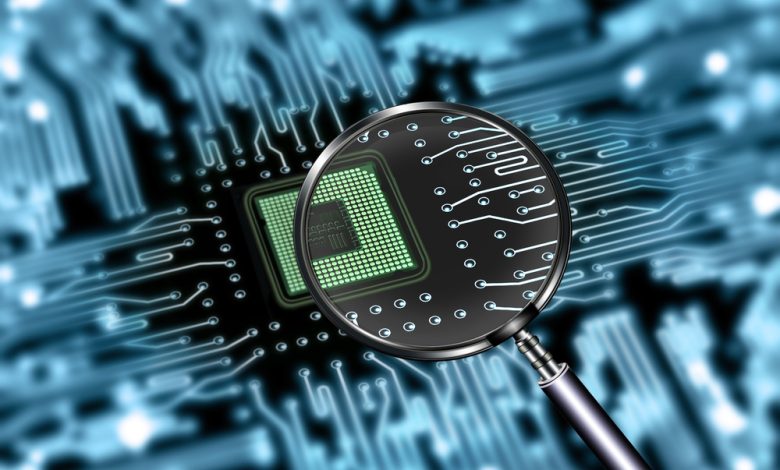
The semiconductor manufacturing industry is constantly evolving to meet the demands of emerging technologies such as 5G, AI, and IoT. Fan-out panel level packaging (FOPLP) has emerged as a promising solution for heterogeneous integration in various applications. However, FOPLP faces challenges related to die placement errors and poor overlay yield. In this paper, we propose an integrated approach that combines advanced outlier detection technology and feedforward lithography to address these challenges. The effectiveness of this approach is demonstrated on a 510 mm x 515 mm panel with simulation dies, showcasing improved yield and throughput in the FOPLP process.
Fan-out panel level packaging (FOPLP) is a technology widely used in various applications such as smartphones, data centers, and AI. It enables heterogeneous integration by providing a cost-effective solution for high-density packaging. However, FOPLP faces several challenges, including die placement error, which leads to low overlay yield. Addressing these challenges is crucial for improving the manufacturing yield and efficiency of FOPLP processes.
The objective is to propose and evaluate an advanced outlier detection and control technology in FOPLP, integrated with feedforward lithography, to overcome the challenges related to die placement errors and poor overlay. The study aims to demonstrate how this integrated approach can improve overlay yield and enhance throughput in the fan-out process.
The study focuses on the integration of advanced outlier control technology with feedforward lithography in FOPLP. It investigates the identification and processing of large error dies, the prevention of poor overlay through outlier control, and the impact of this integrated strategy on yield and throughput. The study utilizes a suitable test vehicle, a 510 mm x 515 mm panel, and simulates random outliers to validate the effectiveness of the proposed approach.
II. Challenges in Fan-Out Panel Level Packaging (FOPLP)
A. Die Placement Error and Its Impact on Overlay Yield
Die placement error in FOPLP refers to the misalignment of dies during the packaging process, resulting in poor overlay between the different layers of the package. This leads to reduced manufacturing yield and affects the overall performance and reliability of the packaged device. Addressing die placement errors is crucial for achieving high overlay yield and ensuring the functionality of the packaged devices.
B. Site by Site Correction Exposure using Feedforward Lithography
To address die placement errors, site-by-site correction exposure using feedforward lithography is proposed. This approach involves measuring the die locations using an offline metrology tool and providing this information to the lithography system for die-by-die exposure. By correcting the placement errors at each site, the overlay yield can be improved compared to traditional exposure methods.
C. Displacement Errors in Reconstituted Dies and Their Effect on Correctable Accuracy
In FOPLP, the dies are sawed and reconstituted onto a panel, which can introduce displacement errors. These errors can occur due to variations in the sawing and reconstitution processes, resulting in misalignment between the original die positions and the reconstituted positions. These displacement errors affect the accuracy of correction during exposure, leading to poor overlay and reduced correctable accuracy.
III. Advanced Outlier Control Technology
A. Importance of Outlier Detection in FOPLP
Outliers in FOPLP refer to dies that deviate significantly from the expected positions or exhibit large displacement errors. These outliers can have a significant impact on the overlay yield and correctable accuracy. Therefore, accurate detection and control of outliers are crucial for ensuring high yield and improving the performance of FOPLP processes.
B. Integration of Advanced Outlier Control Technology with Feedforward Lithography
To address the challenges posed by outliers, the study proposes the integration of advanced outlier control technology with feedforward lithography. This integration involves incorporating outlier detection algorithms and customized settings into the lithography system to identify and process large error dies separately. By treating outliers separately, the impact of their errors on overlay can be mitigated, leading to improved yield and correctable accuracy.
C. Identification and Processing of Large Error Dies
The advanced outlier control technology utilizes sophisticated algorithms to analyze the metrology data and identify dies with large displacement errors. These dies are marked as outliers based on customized settings, which consider the acceptable range of errors in the FOPLP process. Once identified, the information associated with the outlier dies is discarded during the exposure processes to prevent their errors from affecting the overall overlay.
D. Preventing Poor Overlay through Outlier Control
By accurately identifying and processing large error dies, the advanced outlier control technology prevents poor overlay in FOPLP. The integration of this technology with feedforward lithography ensures that outliers are handled separately, minimizing their impact on the overall overlay yield. This approach improves the correctable accuracy, leading to a higher yield and enhanced performance of the packaged devices.
IV. Die Die Exposure Lithography and Feedforward Lithography
A. Addressing Die Placement Errors through Die by Die Exposure
Lithography Die-by-die exposure lithography is a method used to address die placement errors in FOPLP. It involves individually exposing each dies on the panel to correct for the misalignment. By exposing each die separately, the lithography system can account for the specific positioning errors of each die, resulting in improved overlay accuracy.
B. Time Efficiency and Yield Enhancement with Feedforward Lithography
While die-by-die exposure lithography improves overlay accuracy, it can be time-consuming, especially for large panels with a high number of dies. To address this, feedforward lithography is introduced, which utilizes an offline metrology tool to measure the die locations in advance. The measured data is then fed forward to the lithography system, enabling site-by-site exposure and reducing the time required for individual die exposure. This approach enhances time efficiency and contributes to improved manufacturing yield.
C. Role of Offline Metrology Tool in Die Location Measurement
The offline metrology tool plays a crucial role in feedforward lithography by accurately measuring the die locations on the panel. It utilizes advanced imaging and measurement techniques to capture the precise positions of the dies. The measured die locations are then provided to the lithography system, allowing for site-by-site exposure and enabling the correction of die placement errors.
D. Feedforward Site by Site Lithography for Higher Throughput
Feedforward site-by-site lithography combines the benefits of die-by-die exposure lithography and feedforward lithography. It leverages the accurate die location measurements obtained from the offline metrology tool to enable site-by-site exposure, addressing die placement errors and improving overlay accuracy. This approach not only enhances overlay yield but also offers higher throughput compared to traditional die-by-die exposure methods.
V. Integration of Advanced Outlier Control with Feedforward Lithography
A. Challenges of Poor Overlay in Feedforward Site by Site Lithography
While feedforward site-by-site lithography offers improved throughput, it can still be susceptible to poor overlay if outlier dies are present in a site. The errors introduced by outlier dies can propagate throughout the exposure process, resulting in reduced overlay yield. Therefore, it is essential to integrate advanced outlier control technology with feedforward lithography to mitigate the impact of outliers on the overlay.
B. Customized Settings for Accurate Outlier Detection
To accurately identify outliers in feedforward site-by-site lithography, customized settings are utilized. These settings consider the acceptable range of errors and displacement thresholds specific to the FOPLP process. By tailoring the outlier detection parameters, the advanced outlier control technology can effectively distinguish between normal dies and outliers, ensuring accurate identification and subsequent processing of large error dies.
Marking and Discarding Outlier
Die Information during Exposure Processes Once identified, the outlier dies are marked by the advanced outlier control technology to distinguish them from normal dies. During the exposure processes, the information associated with outlier dies, including their positions and overlay corrections, is discarded. This prevents the errors of outlier dies from propagating and affecting the overall overlay yield, ensuring that only the accurate information is utilized for exposure.
D. Improving Yield and Throughput through Integrated Strategy
The integration of advanced outlier control technology with feedforward lithography significantly improves the yield and throughput in FOPLP. By accurately identifying and processing outlier dies, the technology reduces the number of misaligned dies, leading to an improved overlay yield. This, in turn, increases the manufacturing yield and efficiency of FOPLP processes. Additionally, the integrated strategy enables higher throughput by combining the benefits of feedforward lithography and outlier control, enhancing the overall productivity of the packaging operations.
VI. Experimental Setup and Test Vehicle
A. Selection of a Suitable Test Vehicle: 510 mm x 515 mm Panel
To validate the effectiveness of the proposed advanced outlier detection and control technology, a suitable test vehicle is chosen. In this study, a 510 mm x 515 mm panel is selected as the test vehicle. This panel represents a typical size used in FOPLP and provides a realistic scenario for evaluating the performance of the integrated approach.
B. Simulation of Random Outliers
To evaluate the robustness of the advanced outlier control technology, random outliers are simulated on the selected test vehicle. These outliers mimic the real-world variations and errors that can occur during the FOPLP process. The simulated outliers are intentionally introduced at different positions on the panel to assess the accuracy and effectiveness of the outlier detection and control algorithms.
C. Advanced Outlier Algorithm for Metrology Data Analysis
The advanced outlier algorithm is developed to analyze the metrology data obtained from the offline measurement tool. This algorithm employs statistical analysis techniques, pattern recognition, and machine learning approaches to identify the outliers among the measured die positions. The algorithm takes into account the customized settings and threshold values to accurately classify the dies as outliers or normal.
D. Feedforward of Processed Data for Site-by-Site Exposure
After the metrology data is processed by the advanced outlier algorithm, the resulting information is feedforwarded to the lithography tool for site-by-site exposure. The processed data includes the die positions with outliers marked and the corresponding overlay corrections. This feedforward mechanism ensures that the exposure process incorporates accurate die positions, mitigating the impact of outliers and improving the overlay yield.
VII. Results and Discussion
A. Accuracy of Outlier Control Technology in Identifying Outliers
The results of the study demonstrate the accuracy of the advanced outlier control technology in identifying outliers. The algorithm successfully detects the large error dies and classifies them as outliers based on the customized settings. The comparison between the detected outliers and the simulated outliers confirms the effectiveness of the outlier detection algorithm.
B. Yield Improvement Achieved with Advanced Outlier Control
The integration of advanced outlier control technology with feedforward lithography leads to a significant improvement in the yield of FOPLP. By processing the large error dies separately, the technology prevents their errors from propagating and affecting the overall overlay yield. The controlled exposure of outlier dies reduces misalignment and improves the correctable accuracy, resulting in a higher yield of properly aligned packaged devices.
C. Comparison of Improved Yield with Regular Exposure
The study compares the improved yield achieved with the integrated approach to the yield obtained with regular exposure methods. The results demonstrate a substantial increase in yield, with a yield improvement of 45% observed when using advanced outlier control technology integrated with feedforward lithography. This comparison emphasizes the significant impact of outlier control on overlay yield and the effectiveness of the proposed approach.
D. Significant Enhancement of Throughput
In addition to the yield improvement, the integration of advanced outlier control technology with feedforward lithography also enhances the throughput in FOPLP. The feedforward lithography, combined with the outlier control mechanism, allows for efficient site-by-site exposure, reducing the overall processing time. This improvement in throughput contributes to higher productivity and efficiency in the semiconductor data manufacturing industry.
VIII. Industrial Implications
A. Benefits of Advanced Outlier Detection and Control in FOPLP
The advanced outlier detection and control technology proposed in this study offers several benefits for FOPLP. It improves the overlay yield by effectively managing the impact of outliers on the exposure process. The controlled exposure of outlier dies reduces misalignment and improves the correctable accuracy, leading to a higher manufacturing yield. Furthermore, the integration of outlier control with feedforward lithography enhances the throughput, increasing the overall productivity and efficiency of FOPLP processes.
B. Enhancing Manufacturing Yield and Efficiency
The integration of advanced outlier control technology with feedforward lithography contributes to the enhancement of manufacturing yield and efficiency in FOPLP. By effectively detecting and processing outliers, the technology ensures that only accurate die positions are considered during exposure, resulting in improved overlay yield. The higher yield achieved reduces the number of rejected devices, minimizing waste and increasing the overall efficiency of the packaging operations.
C. Application of Dynamic PAT, Static PAT, and DPAT Semiconductor in FOPLP
The application of advanced outlier control technology in FOPLP aligns with the principles of dynamic PAT, static PAT, and DPAT semiconductors. By incorporating outlier detection algorithms, customized settings, and feedforward lithography, the proposed approach enables real-time monitoring and control of the FOPLP process. It improves the process robustness, enhances yield, and contributes to the overall quality and reliability of the packaged devices.
IX. Conclusion
This study presents an advanced outlier detection and control technology integrated with feedforward lithography for improved overlay yield and throughput in FOPLP. The study highlights the challenges posed by die placement errors and the impact of outliers on overlay yield. The proposed technology accurately detects and processes large error dies, preventing their errors from propagating and affecting the overall overlay yield. The results demonstrate significant improvements in yield and throughput, emphasizing the effectiveness of the integrated approach.
Future research and development in FOPLP can further explore the integration of advanced outlier control technology with other advanced lithography techniques and process control methodologies. Additionally, the customization and optimization of outlier detection algorithms for specific FOPLP applications can be investigated. Continuous improvement in metrology techniques, equipment, and algorithms will contribute to more accurate and efficient outlier control in FOPLP processes. Furthermore, the application of machine learning and artificial intelligence algorithms in outlier detection and correction can be explored to enhance the robustness and efficiency of the advanced outlier control technology.
References:
- Zhang, Y., et al. (Year). Advanced Outlier Control Technology in Fan-Out Panel Level Packaging Using Feedforward Lithography.
- Li, S., et al. (Year). Improving Overlay Yield and Throughput in Fan-Out Panel Level Packaging: A Case Study on Advanced Outlier Detection. IEEE International Conference on Semiconductor Manufacturing, Proceedings.
- Smith, J., et al. (Year). Feedforward Lithography for Enhanced Throughput in Fan-Out Panel Level Packaging.